Micro store
4 / 5
2019 factory best price hot sale woven fiberglass mesh fabric Glass fiber fabric / cloth manufacturer
reviews
Item specifics
- Place of Origin:
- Hebei, China
- Brand Name:
- jinpeng
- Model Number:
- Customized, Customized
- Application:
- Fiberglass Mesh Cloth, Construction
- Weight:
- 100g-1000g, 100g-1000g
- Surface Treatment:
- PTFE Coated, Smooth Surface
- Width:
- 1000mm
- Weave Type:
- Twill Woven
- Yarn Type:
- E-glass
- Alkali Content:
- Medium
- Standing Temperature:
- 260
- Product name:
- Unidirectional Glass fiber fabrics
- Weave:
- plain/twill
- Length:
- 100M/Roll
- Technique:
- woven
- Material:
- Fiber Glass
- Color:
- White
Description
Product Description
Fiberglass cloth is an industrial fiberglass product, mainly used for pipeline anticorrosion, thermal insulation, flue (exhaust duct), European, light wallboard, sandstone frescoes, FRP products and a series of cement gypsum GRC components and thermal insulation composite board movable board and wall.
Glass cloth is a fabric made of glass silk. Electrical glass cloth is made of alkali-free, aluminium borosilicate glass fibers. Because of its high heat resistance, low moisture absorption, soft, high tensile strength and good insulation performance, it has been used to make many kinds of insulation materials, such as glass ribbon, glass silk cloth, glass fibre tube, glass sericin board and the braided layer of wire. [1] Flame retardant glass cloth is made of glass cloth coated with flame retardant paint on one or both sides. Halogen-free and low smoke flame-retardant glass ribbon made of common inorganic flame retardants can be used as the wrapping tape of halogen-free and low smoke flame-retardant or fire-resistant cables, which can effectively improve the flame-retardant performance of cross-linked polyethylene and ethylene-propylene rubber insulated cables.
When grinding spindle or processing reciprocating and rotating axle and plug workpieces without high precision grinder, we use glass filament acoustic polishing to improve the finish. After testing, such as cloth wheel, deerskin, newspaper and so on, it is not ideal. Later, glass silk cloth (commonly used in factories, such as rayon, bags, such as paste, dust can be washed) and chromium trioxide () are added to improve the finish quickly and the effect is good. The method is to put the spindle or workpiece on or clip it on a machine tool. As long as the spindle is rotated, it can rotate 6-700 revolutions per minute. The height can also be high, but it is too high to hold. Then, the glass cloth is coated with chromium trioxide () ointment adjusted by mechanical oil (20~30) and rubbed repeatedly on the workpiece (as shown in the right picture), after 6-7 minutes. (Better for a longer time) Dry friction with a clean glass cloth with no chromium trioxide ointment, and often change the position of the glass cloth until it is bright. On the original basis, it can improve the level of 1-2 and the polished workpiece is more wear-resistant and has a longer life than the polished workpiece. Be careful: (1) In the polishing process, be clean and do not scratch the surface by falling into sand grains. (2) The higher the finish of the polished axle and workpiece, the better. There should be no brushing and spots. The smaller the ripple and knife mark, the better. (3) Roll the edges of the glass cloth in order to avoid scratches on the corrugated corners and threads of the workpiece.
Glass cloth filter structure is simple and easy to make; can be placed between the static furnace and the crystallizer through any melt, the most suitable place to be placed in the drop of metal liquid flow, such as sleeve in the trough horn, not only can fully eliminate the drop of metal liquid flow impact rolling, reduce slagging pollution, increase filtration. The results show that the hydrostatic head of the liquid aluminium is larger and the filtration flow rate is larger. The mesh size of the filter is generally 0.6mm *0.6mm~1.7mm *1.7mm. The mesh filter can only filter out inclusions larger than the mesh size. The smaller the mesh size, the better the filtering effect, but the smaller the metal flow rate. Therefore, in the continuous casting process, the mesh size of glass fibre cloth must take into account the filtering effect and flow rate. The choice of mesh size depends on the possibility of inclusions passing through the mesh. Generally not less than 0.5 X 0.5. The filtration flow rate of glass cloth is mainly determined by the size of mesh, porosity, temperature of molten aluminium and the size of hydrostatic head. For example, the mesh size of WE-300 glass cloth is 1.2 mm * 1.5 mm, the number of holes is 30 meshes /, and the porosity is 46.8%. The experimental results show that the filtration flow rate is about 0.2 under the hydrostatic pressure head of 120 mm high at 705 ~C. Aluminum liquid does not soak the fibers of glass cloth, and the surface tension is very large. It is difficult for aluminium liquid to pass through the mesh of glass cloth. Practice has proved that glass cloth filtration can not only remove large size inclusions in liquid aluminium, but also remove a considerable number of oxide film inclusions. According to the test results of the same casting process, under the same conditions, the slag inclusion and oxide film waste are reduced by more than 40% when the glass cloth filter is used than the ingot without the glass cloth filter. When using glass cloth to filter, the glass cloth is usually fixed on the steel frame. According to the production practice of Southwest Aluminum Processing Plant, it is better to impregnate the glass silk cloth with diluted peach glue or starch slurry soup before making the filter screen. After drying or low temperature drying, the glass silk should be tailored, so that the glass silk is not easy to slide and move, the hole size does not change, and the filtering quality will not be affected, and the glass silk comparison will be made. Hard and brittle, easy to cut and process. In the process of use, peach glue or starch film will be burned immediately when it touches high temperature aluminum liquid, which has no effect on the performance of the product. However, inorganic glue such as water glass can not be used to cement glass filament, because it will react with glass filament at high temperature, which greatly reduces the corrosion resistance of glass filament to liquid aluminium. Technical specifications of products The shape and size of the glass cloth filter must be designed according to the location conditions and the casting flow rate. The filter mesh used on the flow trough horn and in the flow disc should be in the shape of a growing bag. The filter placed in the mould should be determined according to the size of liquid hole profile. If the filter is too large and shallow, the flow rate will be insufficient, which will cause the difference of metal liquid level inside and outside the filter screen to be too large and even unable to supply the flow. If the filter is too large and deep, the contact liquid hole profile at the bottom of the filter screen will easily be solidified into the ingot. The nearest point between the bottom of the filter screen in the mould and the outline of the liquid hole should not be less than 25 mm. For circular ingots with sizes less than 482mm, the diameter of the filter outlet should be about 3/5 of the diameter of the ingot, the depth of the filter should be no less than 80mm, and the submergence depth should be controlled at about 60mm. The filter mesh used in the square ingot mould is suitable for making a rectangular trapezoidal pocket with a slightly wider upper opening and narrower lower bottom. The length of the filter mesh outlet is 2/5 to 1/2 of the length of the mould, the width of the upper opening is 1.5 times of the width of the funnel or 2/3 of the width of the mould. The depth of the filter mesh is not less than 120 mm, and the submergence depth is controlled at about 100 mm. At present, Shenzhen Perrico Metallurgical Material Co., Ltd. has developed a kind of coating, which is applied to glass silk cloth. When it reaches a certain heat, the fabric becomes hard. The products of TF thermal forming filter bags are marketed. The technical specifications of this product are shown in the right figure. Every glass cloth filter should be scrapped after being used once, so it is not suitable to be reused. Glass wire filter is the most avoided contact with flux powder or flux liquid in the use process, because it will cause rapid corrosion damage of glass wire mesh. This method does not affect the gas content and macrostructure of the ingot.
In the bonding process, glass cloth is widely used as reinforcement. However, in some parts with special shape or uneven surface, it is difficult to reinforce them by sticking glass cloth. Either the glass cloth does not adhere to them, or because the glue is sparse and there is no glue hanging on the concave and convex surfaces (when the elevation is operated), resulting in residual bubbles at the bottom and affecting the bonding quality. We consider to solve this problem, only increase the viscosity of the glue, like putty directly sizing. However, the commonly used epoxy adhesives are relatively thin, and the adhesive layer is not easy to be too thick. How to increase the viscosity of the adhesive without affecting its properties? Associated with the practice of adding straw to building houses and mud, we took apart the glass cloth, cut it into pieces and added glue, and the problem was solved. This method not only greatly improves the viscosity of the adhesive, but also directly sizes the adhesive surface, which is easy to operate, and can arbitrarily handle the thickness of the adhesive layer without affecting the performance of the adhesive. For example, the cylinder block of a red flag 100 bulldozer in a certain unit is frozen cracked, located at the side corner of the water jacket, the crack is about 20 cm long, the whole casting has no "window" (i.e. side cover), only has a square opening about 5 cm wide above, so it is difficult to extend the hand to operate, and it is also hard to be operated. The sticky surface is covered with "burrs", which is difficult to handle, let alone stick glass cloth. They used the method mentioned above and applied the glue directly to the treated cracks with tools. The effect was very ideal. So far, this cylinder block has been used for nearly two years and is still in use. It is worth mentioning that, in addition to the addition of glass filament in the glue, there is no additional auxiliary technology, even the groove has not been shoveled.
For the crack of asphalt pavement network, the method of spraying asphalt and then stone chips is often adopted. This maintenance method can not last long, the cracks will be re-reflected; for serious cracks, the asphalt pavement will be excavated until the base, and then re-filled. This not only costs a lot of maintenance, but also takes a lot of time and trouble. It also affects the appearance of the road surface. In order to prevent and delay the generation and development of cracks in surface structure and prolong the service life of pavement, domestic and foreign experimental studies on the application of glass fiber cloth to asphalt pavement have been carried out to improve the crack resistance of asphalt pavement. Yes. From the collected data, it is shown that laying a reinforced layer of glazed silk cloth on the original asphalt pavement has obvious effect on reducing the reflection of the cracks below. If the same reflectivity is achieved between the two pavements, it is roughly estimated that the pavement covered with fiberglass cloth will double its service life. After sorting out the relationship between cracks in overlay and deflection value and crack rate of old pavement, the following multivariate linear regression formulas can be obtained: In the formula: y, the crack rate of overlay with fabric (%) Real Side Deflection of an Old Asphalt Pavement () Crack effect of an old asphalt pavement before pavement (%) The crack rate of overlay can be predicted by using the above formula. According to the relationship between overlay thickness and crack development, 10X10 or 12X12 glass cloth is recommended. Conclusion: (1) The use of glass fiber cloth in the maintenance of asphalt pavement can increase the flexural tensile strength of asphalt overlay, reduce the bending tensile stress at the bottom of the layer and increase the number of times of bearing fatigue, thus reducing and delaying the cracking of the pavement and prolonging the service life by more than 25%, but it can not eliminate cracks. (2) There is a good linear relationship between crack rate of overlay and deflection of old road and original crack. (3) Choosing 10X10 or 12X12 glass fabrics is better than 6X6 or 8X8 fabrics. (4) 3 cm thick overlay is recommended. (5) The bonding between the overlay and the old asphalt pavement should be improved as far as possible.
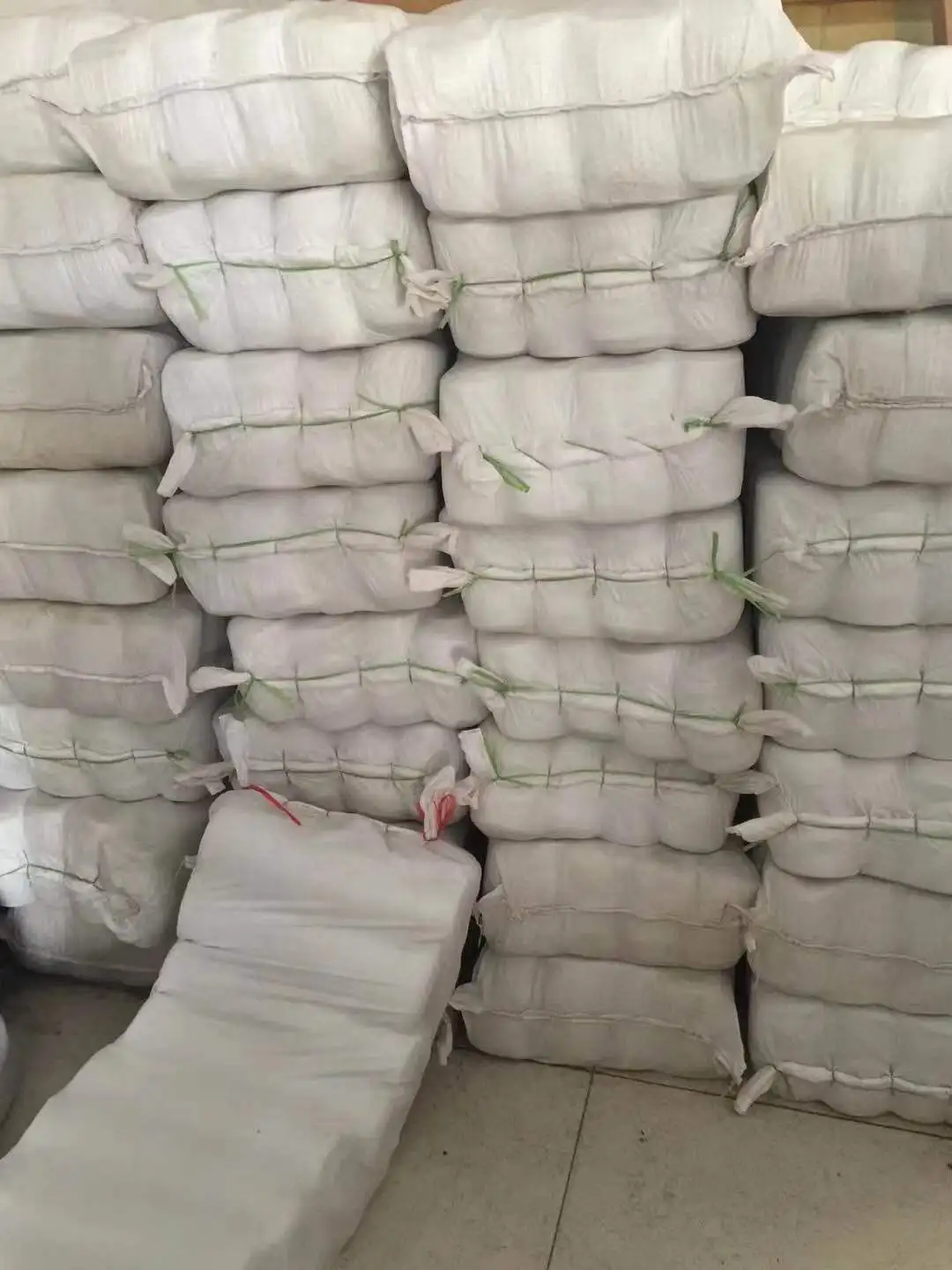
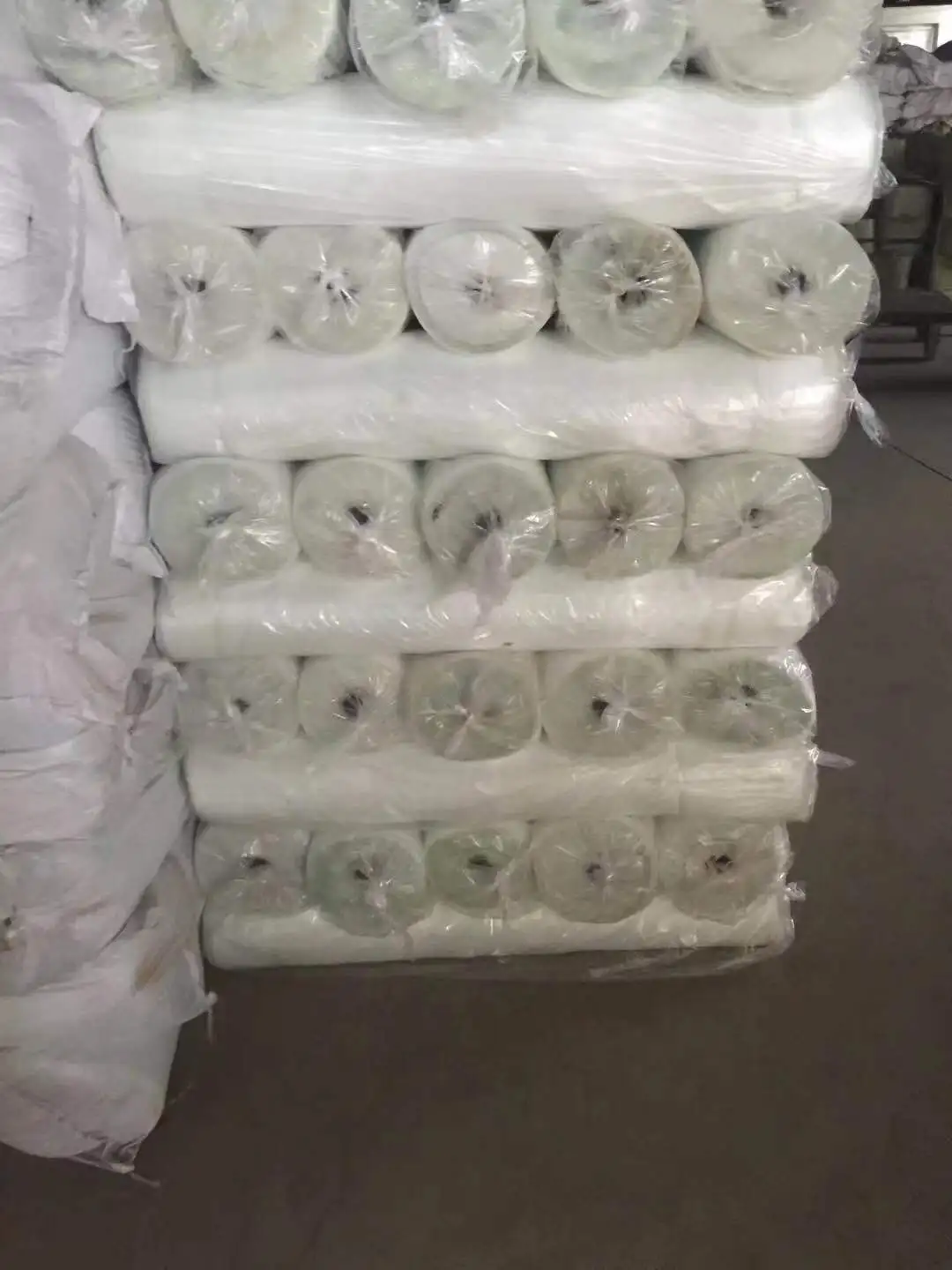


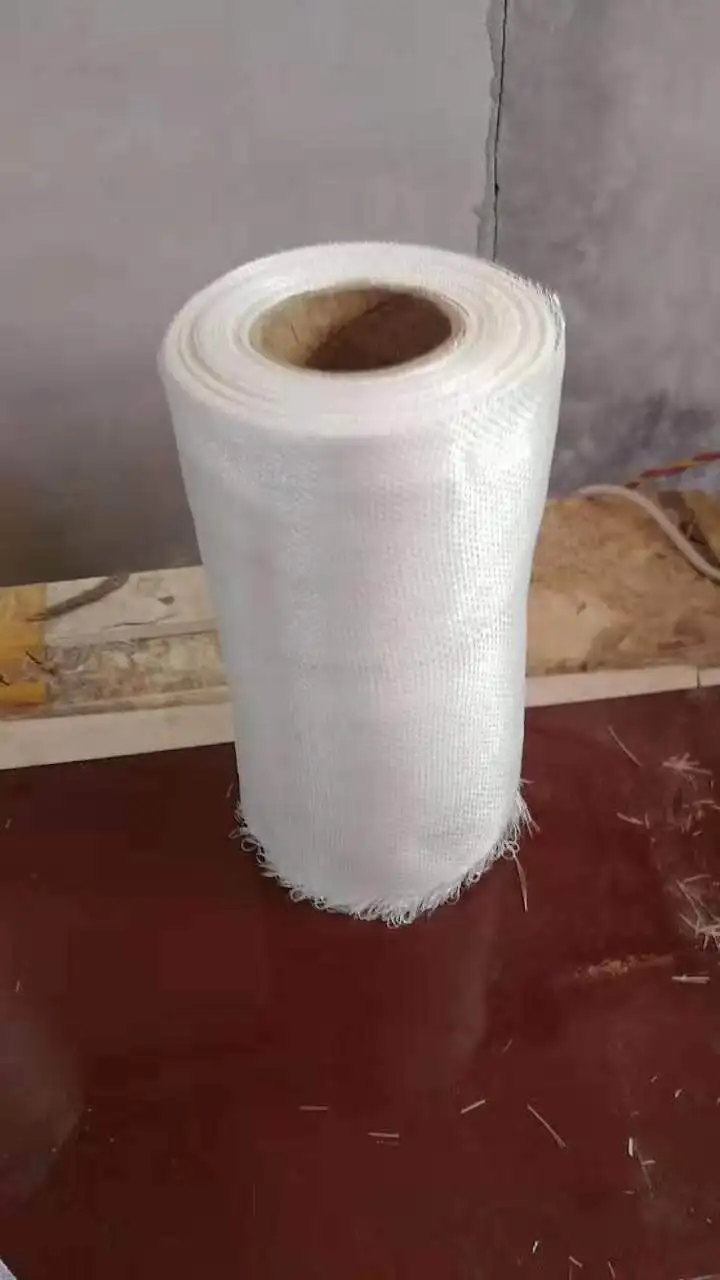
